Heatseal instructions
Embroiderybadge UK |
Heat Press | Heat Presses for cap | ||||||
Heat press with either top or bottom heat. | Heat press with dual top and bottom heat | Cap heat press with either top or bottom heat. | Cap heat press with dual top and bottom heat | |||||
Temp Top or Bottom (°C) | Time | Temp Top/Bottom (°C) | Time | Temp Top or Bottom (°C) | Time | Temp Top/Bottom (°C) | Time | |
Embroidered badge | 130°-140° | 20 – 30 seconds | 130°-140° | 15-20 seconds | 140°-160° | 2 x 10-20 seconds | 140°/160° | 45 seconds |
Embroidered Chenille badge | 130°-140° | 25-35 seconds | 130°-140° | 15-20 seconds | 140°-160° | 2 x 10-20 seconds | 140°/160° | 45 seconds |
Embroidered 3D Puff badge | 130°-140° | 25-35 seconds | 130°-140° | 20-30 seconds | 140°-160° | 2 x 10-20 seconds | 140°/160° | 45 seconds |
Woven badge | 130°-140° | 20-30 seconds | 130°-140° | 15-20 seconds | 140°-160° | 2 x 10-20 seconds | 140°/160° | 45 seconds |
Woven label | 130°-140° | 15-20 seconds | 130°-140° | 15 seconds | 140°-160° | 2 x 10-20 seconds | 140°/160° | 45 seconds |
Sublimation & Sublistitch badge | 130°-140° | 20-30 seconds | 130°-140° | 15-20 seconds | 140°-160° | 2 x 10-20 seconds | 140°/160° | 45 seconds |
Metaprint & TPU badge | 130°-140° | 10-15 seconds (low pressure) | 130°-140° | 10-15 seconds | 140°-160° | 2 x 10-20 seconds | 140°/160° | 45 seconds |
PVC/Rubber badge | 140°-150° | 40 seconds | 140°-150° | 40 seconds | 140°-160° | 2 x 30 seconds | 140°/180° | 60 seconds |
Silicon badge | 130°-140° | 25-30 seconds | 130°-140° | 20-25 seconds | 140°-160° | 2 x 25 seconds | 140°/160° | 50
seconds |
When it comes to using presses that only heat from the top, it is important to note that instructions may vary for each machine. To ensure a strong bond between the badge and the garment, we recommend flipping the badge with the garment and applying heat from the opposite side for the same duration. Prior to this, it is also essential to preheat the garment by performing a blank press for 5-10 seconds, eliminating any moisture.Now for dual heating machines, please use a silicone pad or teflon sheet to protect the front of the badge from direct heat. PLEASE NOTE: the guidelines we’ve shared on our site are more like starting points. Every machine and fabric is a bit different, and honestly, there’s no one-size-fits-all solution. We totally understand how frustrating it can be to find the perfect settings, so we’re here to encourage you to experiment a little. Play around with the temperature and timing to find what works best for your unique situation. Trust us, a little tweaking here and there can make all the difference. Thanks for your understanding and happy experimenting! Cap pressesFor cap presses that heat only from the top, we advise preheating the cap for 10 seconds before applying heat for 12-18 seconds, depending on the badge. However, it’s important to consider the material of the badge as materials such as 3D foam and TPU are unsuitable for these presses as they may melt. We strongly recommend using the Hotronix 360 IQ Hat Heat Press, which is unparalleled in the market. Temperature settings for this heat press vary depending on the type of hat. Still, we recommend 90°C on top and 140°-160°C on the bottom. Foam caps, on the other hand, require a lower bottom temperature and higher top temperature. |
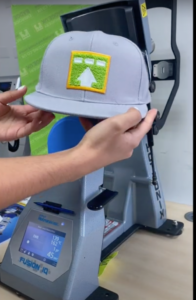
Washability
Embroiderybadge UK |
Temperature | Time | Usage |
Embroidered badge | 40-45 degrees max | Wash for max. 45 min | 30-40 times |
Embroidered Chenille badge | 40-45 degrees max | Wash for max. 45 min | 30 times |
Embroidered 3D Puff badge | 40-45 degrees max | Wash for max. 45 min | 30 times |
Woven badge | 40-45 degrees max | Wash for max. 45 min | 30-40 times |
Woven label | 40-45 degrees max | Wash for max. 45 min | 50-70 times |
Sublimation & Sublistitch badge | 40-45 degrees max | Wash for max. 45 min | 30 times |
Metaprint & TPU badge | 40-45 degrees max | Wash for max. 45 min | 10 times |
PVC/Rubber badge | 40-45 degrees max | Wash for max. 45 min | 10 times |
Silicon badge | 40-45 degrees max | Wash for max. 45 min | 10 times |
Important: No tumble dry for all badges. Please be aware that the instructions vary for every machine. These are just generic instructions, we strongly advise testing the badges on your garment first. We are not responsible for any damage or wrong usage. |
A basic heat-seal guide to applying Badges/patches:
To apply badges or patches, it is important to follow certain steps.
- First, preheat the heat press to the appropriate temperature for your fabric and badge by consulting the manufacturer’s instructions.
- Once the heat press is preheated, place the badge on the fabric, making sure it is straight and not twisted. To protect the badge and fabric from heat, cover the badge with a pressing cloth.
- Next, place the fabric with the badge and pressing cloth into the heat press, following the manufacturer’s instructions for positioning and pressure.
- Run the heat press machine for the recommended duration, applying heat and pressure to the badge.
- After the heat-sealing process is complete, remove the fabric from the machine and allow the badge to cool. It is important to not handle the badge until it has completely cooled down.
- Once the badge is cool, gently remove the pressing cloth to reveal the securely affixed badge.
To avoid mistakes, it is highly recommended to perform a sample run before proceeding with the final heat-sealing process. This can be achieved by ordering a few extra badges or caps to test with. By doing a sample run, you can avoid potential issues and save yourself from unnecessary hassles. Videos on heat-sealing and other methods can be found by scrolling down our information page.
Please note that the following are recommended guidelines for heat sealing badges based on best practices. These instructions are intended to serve as a basic guide and may need to be adjusted based on specific materials, equipment, and conditions. It is advisable to conduct a test seal to determine the optimal settings for your particular situation. We do not guarantee that these recommendations will be suitable for all badge types or fabrics, and we are not liable for any damage or unsatisfactory results that may occur from following these guidelines. Users should proceed with caution and at their own risk!
For Raised Silicone Transfers, we suggest the following instructions:
- Pre-heat press to 150°C (lower for polyester clothing)
- Place garment under heat press and ensure the garment is flat so that the heat press applies even pressure.
- Place DTF transfer in desired position.
- Press at a medium to firm pressure for 15 seconds.
- For best results remove the garment from the heat press and allow transfer to cool COMPLETELY before peeling film from the transfer in one smooth rolling motion.
For DTF and Stitch Effect Transfers we suggest the following instructions:
- Pre-heat press to 155°C (120°C when pressing on polyester).
- Place garment under heat press and ensure the garment is flat so that the heat press applies even pressure
- Place DTF transfer in desired position.
- Press at a medium to firm pressure for 10 seconds.
- Can be peeled hot, however for best results remove the garment from the heat press and allow transfer to cool before peeling film from the transfer in one smooth rolling motion.
- Place garment back under press as before and re press a second time for 5 seconds using the release paper to cover the print (release paper provided).
PLEASE NOTE: The above times and temperatures are provided as a guide only. On first use of our DTF transfers or when pressing new types of fabric we suggest performing tests!